Translate
lunes, 22 de abril de 2013
Reflexiones flexográficas II: ¿Puedo mejorar?
Mi padre era un autodidacta, un hombre que se hizo a sí mismo con grandes dosis de esfuerzo, ilusión y humildad. Lo hizo con tesón hasta conseguir destacar en aquello que mas le apasionaba: la electrónica. Cuando la situación económica le obligó a emigrar, se llevó consigo la base técnica y la actitud necesarias para abrirse camino en esa profesión; un entorno muy distinto al que tengo yo y al que probablemente tendrá quien está ahora mismo leyendo estas reflexiones. De mi padre me quedaría con muchas cosas, pero sobre todo con sus ansias por aprender y con su disposición por mejorar continuamente.
Me acordé de mi padre cuando me decía recientemente un empresario de artes gráficas dedicado a la impresión de embalaje flexible que su empresa apuesta por la "mejora continua" en todos sus procesos para obtener las necesarias "eficacias y eficiencias" en la producción; la mejor estrategia para alcanzar los objetivos generales y con ello la mayor rentabilidad de su negocio. Nada que objetar a esa perspectiva, por supuesto.
Ser "eficaz" es ser capaz de realizar un cometido y ser "eficiente" es conseguir o superar con ello un resultado predefinido. Contextualizando esto en el entorno de las artes gráficas en general y en la impresión flexográfica en particular, nos encontramos con que no es nada fácil obtener un resultado óptimo en la producción gráfica, básicamente por que la eficiencia y eficacia se ven muy dificultadas por factores de difícil control.
Volviendo a mi padre; él trabajaba con valores resultantes "predecibles", así cuando fabricaba una fuente de alimentación, sabía que entraría una corriente alterna de 100/220V, y tal como estaba configurada, esta le daría una salida de corriente continua de 5/12V, por poner un ejemplo. Para ello tenía definidos unos componentes necesarios que darían ese resultado; un resultado predecible y necesario para que el aparato al que se conectaría pudiera realizar su función.
La "función", en este caso gráfica, de un envase o embalaje flexible es la de generar un impacto visual atractivo que permita captar la atención del cliente en el punto de venta, informarlo sobre el contenido del envase y crearle, en conjunto, una imagen positiva de marca. Estas necesidades delimitan los retos que debe asumir cualquier impresor flexográfico y en los últimos años, esos retos se han visto muy reforzados por diversos motivos.
Como pasa en la electrónica y salvando las distancias con el contexto gráfico, obviamente en la impresión flexográfica también es preciso cumplir con la funcionalidad a la que está dirigida, sin perder de vista las muchas condicionantes que se dan y que son propias del sistema de impresión, así como las implicaciones que estas condicionantes tienen sobre el objetivo de obtener un resultado que cumpla con los requisitos establecidos por el cliente y que esté alineado con la previsión de costes y márgenes correspondientes.
Con todo ello, la predecibilidad en la flexografía es un factor igualmente determinante, ya que sin predecir un resultado, difícilmente se podrá ser eficaz y por extensión eficiente, por lo que el único camino que nos puede llevar a un resultado satisfactorio pasa por ser capaces de conocer como imprime nuestra máquina y cuales son sus límites y posibilidades reales, adelantándonos a las dificultades que se presentarán y estableciendo con antelación los ajustes necesarios.
En este sentido y como profesional que cree conocer las tecnologías Kodak y otras complementarias existentes en el sector, me atrevo a asegurar que con el conjunto de estas soluciones el impresor dispone ya de las herramientas necesarias y adecuadas para conseguir el objetivo, solo falta añadir las necesarias dosis de esfuerzo, ilusión y disposición de mejora que posiblemente hayamos ido dejando por el camino por algunas decepciones pasadas, unas decepciones que tal vez fuesen el resultado de utilizar unos planteamientos equivocados o tal vez fuese otra la razón. No obstante, lo fundamental es hacerse una pregunta..., ¿puedo mejorar?.
Yo creo que siempre se puede mejorar en flexografía y ahora mas que nunca, el primer paso es querer hacerlo.
sábado, 20 de abril de 2013
Reflexiones flexográficas
Muchos años después de que la flexografía diera un salto importantísimo con la aparición de las tecnologías de planchas LAM, un salto que recientemente ha tenido un nuevo impulso con la irrupción de innovaciones como Kodak Flexcel NX, es ahora que vemos como este sistema de impresión se ha convertido definitivamente en una alternativa real al huecograbado, siendo capaz de obtener unos niveles de calidad semejantes, pero con las ventajas añadidas que ofrece este sistema de impresión.
Pues bien..., comentaba hace unos días a un impresor que hay veces en las que pienso que los profesionales que llevamos acumulados muchos años en este sector, tantos que ya nos empieza a costar reconocerlos, llevamos (no sin un cierto orgullo) alguna que otra cicatriz moral por las dificultades vividas a la hora de cumplir con determinadas expectativas de calidad y productividad en la impresión durante ese tiempo.
Y es que ciertamente hemos sido testigos y partícipes de esa gran evolución en la flexografía, pero víctimas también de nuestras propias dificultades para entender este nuevo contexto y evolucionar con ello adecuadamente. Tanto es así que, desde mi punto de vista, vemos pasar avances y mas avances tecnológicos sin haber sido capaces de implementarlos correctamente y sin sacar de ellos el rendimiento que sin duda pueden generar.
Creo que hemos tenido una cierta tendencia a obsesionarnos en un enfoque equivocado sobre nuestro objetivo, tal vez sea ese el motivo por el que nos empeñamos en compararnos con el punto de referencia ideal, aquel que siempre hemos querido alcanzar en flexo y cuando lo hemos conseguido (casi siempre por casualidad y a costa de horas, material y coste desperdiciados), lo hemos utilizado para, de algún modo, satisfacer nuestro maltrecho ego profesional diciendo lo de... "estamos imprimiendo con una calidad de huecograbado", o aquello otro de..."estamos al nivel del offset". Y con eso damos por entendido que el éxito ha sido incontestable y estamos en el camino correcto para alcanzar nuestros objetivos de competitividad.
Pero no..., es que hay algo que parece no acabar de entenderse, cierto es que no en todas las empresas, pero sí en muchas..., y es que el reto no es imprimir como el offset, ni tampoco hacerlo como el huecograbado, el reto es imprimir con mucha calidad, sí..., pero también hacerlo de manera suficientemente eficiente como para con ello rentabilizar la producción y alcanzar el rendimiento en el resultado que realmente exige el comprador de impresión y que exige también la imprescindible rentabilidad del impresor.
Y cuando se dice esto, es entonces que cuesta reconocer esa realidad, ya que por lo visto TODOS trabajamos para ser mas rentables, eso por supuesto..., y la prueba de ello es que exprimimos el ahorro de costes en factores tan "decisivos" en la impresión (entiéndase la ironía) como el coste de la preimpresión, que en la mayor parte de paises es suministrada por servicios externos, creyendo con ello que con ahorrar un 10% en el precio de las planchas vamos a reducir sensiblemente los costes totales con una convicción basada en que el riesgo de una baja calidad de esta parte del proceso no es peligroso, y que nuestra habilidad y buen hacer en la máquina impresora podrá corregir las posibles deficiencias o inconsistencias que se produzcan en la impresión; eso sí... olvidando por completo que el coste de un juego de planchas respecto del global de un tiraje de embalaje flexible en flexografía pueda ser proporcional al mordisco de un niño a una manzana, entendiendo la manzana como el total que supone esa fabricación. Y al final, el riesgo se hace presente en forma de un exceso de mermas por una mala preimpresión que supone mucho mas coste que ese 10% del mordisco que queremos ahorrar.
Entiendo la mirada un tanto extraña del impresor al que confesé este parecer, pero es que creo que si la impresión flexográfica está en "primera división" y quiere jugar con los mejores, esto exige compromisos, sin duda alguna los de dar el mismo nivel en calidad, pero también de consistencia y repetibilidad de la misma. No es dificil de aceptar entonces que en flexografía ese es un reto muy importante, que implica el trabajar de otra manera y reconocer la necesidad de cumplir con unas reglas en producción basadas en unos parámetros definidos, como respetar la densidad de referencia, trabajar con un anilox limpio y adecuado, unas tintas en buenas condiciones, unas viscosidades controladas, unos adhesivos correctos, una buena tecnología de planchas o sacar el densitómetro del fondo del cajón, quitarle el polvo acumulado por el poco uso y dejar de lado el ajuste del color basado en el buen criterio colorimétrico del ojo del maquinista, con todo el respeto al maquinista, por supuesto.
Este es el mejor modo de abaratar los costes: el "ser eficientes imprimiendo correctamente", esto nos permitirá aprovechar las ventajas que esas nuevas tecnologías nos aportan, convirtiendo al proveedor de preimpresión en una aliado que nos ayude y aconseje en ese objetivo, no en un simple suministrador de planchas.
Sin dejar de aceptar que estas opiniones puedan ser discutibles o matizables, espero que al menos invite a reflexionar sobre como debemos plantear los distintos procesos que participan en la impresión flexográfica, sobre todo ahora que el nivel de exigencia es tan alto que resulta muy difícil mantener margenes razonables.
Pues bien..., comentaba hace unos días a un impresor que hay veces en las que pienso que los profesionales que llevamos acumulados muchos años en este sector, tantos que ya nos empieza a costar reconocerlos, llevamos (no sin un cierto orgullo) alguna que otra cicatriz moral por las dificultades vividas a la hora de cumplir con determinadas expectativas de calidad y productividad en la impresión durante ese tiempo.
Y es que ciertamente hemos sido testigos y partícipes de esa gran evolución en la flexografía, pero víctimas también de nuestras propias dificultades para entender este nuevo contexto y evolucionar con ello adecuadamente. Tanto es así que, desde mi punto de vista, vemos pasar avances y mas avances tecnológicos sin haber sido capaces de implementarlos correctamente y sin sacar de ellos el rendimiento que sin duda pueden generar.
Creo que hemos tenido una cierta tendencia a obsesionarnos en un enfoque equivocado sobre nuestro objetivo, tal vez sea ese el motivo por el que nos empeñamos en compararnos con el punto de referencia ideal, aquel que siempre hemos querido alcanzar en flexo y cuando lo hemos conseguido (casi siempre por casualidad y a costa de horas, material y coste desperdiciados), lo hemos utilizado para, de algún modo, satisfacer nuestro maltrecho ego profesional diciendo lo de... "estamos imprimiendo con una calidad de huecograbado", o aquello otro de..."estamos al nivel del offset". Y con eso damos por entendido que el éxito ha sido incontestable y estamos en el camino correcto para alcanzar nuestros objetivos de competitividad.
Pero no..., es que hay algo que parece no acabar de entenderse, cierto es que no en todas las empresas, pero sí en muchas..., y es que el reto no es imprimir como el offset, ni tampoco hacerlo como el huecograbado, el reto es imprimir con mucha calidad, sí..., pero también hacerlo de manera suficientemente eficiente como para con ello rentabilizar la producción y alcanzar el rendimiento en el resultado que realmente exige el comprador de impresión y que exige también la imprescindible rentabilidad del impresor.
Y cuando se dice esto, es entonces que cuesta reconocer esa realidad, ya que por lo visto TODOS trabajamos para ser mas rentables, eso por supuesto..., y la prueba de ello es que exprimimos el ahorro de costes en factores tan "decisivos" en la impresión (entiéndase la ironía) como el coste de la preimpresión, que en la mayor parte de paises es suministrada por servicios externos, creyendo con ello que con ahorrar un 10% en el precio de las planchas vamos a reducir sensiblemente los costes totales con una convicción basada en que el riesgo de una baja calidad de esta parte del proceso no es peligroso, y que nuestra habilidad y buen hacer en la máquina impresora podrá corregir las posibles deficiencias o inconsistencias que se produzcan en la impresión; eso sí... olvidando por completo que el coste de un juego de planchas respecto del global de un tiraje de embalaje flexible en flexografía pueda ser proporcional al mordisco de un niño a una manzana, entendiendo la manzana como el total que supone esa fabricación. Y al final, el riesgo se hace presente en forma de un exceso de mermas por una mala preimpresión que supone mucho mas coste que ese 10% del mordisco que queremos ahorrar.
Entiendo la mirada un tanto extraña del impresor al que confesé este parecer, pero es que creo que si la impresión flexográfica está en "primera división" y quiere jugar con los mejores, esto exige compromisos, sin duda alguna los de dar el mismo nivel en calidad, pero también de consistencia y repetibilidad de la misma. No es dificil de aceptar entonces que en flexografía ese es un reto muy importante, que implica el trabajar de otra manera y reconocer la necesidad de cumplir con unas reglas en producción basadas en unos parámetros definidos, como respetar la densidad de referencia, trabajar con un anilox limpio y adecuado, unas tintas en buenas condiciones, unas viscosidades controladas, unos adhesivos correctos, una buena tecnología de planchas o sacar el densitómetro del fondo del cajón, quitarle el polvo acumulado por el poco uso y dejar de lado el ajuste del color basado en el buen criterio colorimétrico del ojo del maquinista, con todo el respeto al maquinista, por supuesto.
Este es el mejor modo de abaratar los costes: el "ser eficientes imprimiendo correctamente", esto nos permitirá aprovechar las ventajas que esas nuevas tecnologías nos aportan, convirtiendo al proveedor de preimpresión en una aliado que nos ayude y aconseje en ese objetivo, no en un simple suministrador de planchas.
Sin dejar de aceptar que estas opiniones puedan ser discutibles o matizables, espero que al menos invite a reflexionar sobre como debemos plantear los distintos procesos que participan en la impresión flexográfica, sobre todo ahora que el nivel de exigencia es tan alto que resulta muy difícil mantener margenes razonables.
lunes, 15 de abril de 2013
Innovación tecnológica Flexcel NX para la impresión flexográfica
El consumidor, cada vez más escaso de
tiempo, está mas influenciado por el primer impacto visual del producto
ante la decisión de compra. El minorista tiende a hacer más atractivas
las compras del cliente facilitando el contacto y acceso al producto. Y
los propietarios de marcas invierten en packaging innovador para
reforzar el atractivo en el lineal. Estos buscan, además, una
correlación de colores uniforme entre sustratos, tiradas, ubicaciones y
tecnologías de impresión, más personalización. Los convertidores centran
sus esfuerzos en la calidad, productividad y reducción de costes en un
contexto de respeto al medioambiente y a la marca cada vez más exigente;
quieren una impresión más rentable en tiradas cortas. Kodak responde a estos desafíos con su tecnología Flexcel NX.
Desde mi punto de vista, el concepto de plancha flexográfica
digital tradicional LAM, por su concepto técnico, tiene ciertas dificultades para responder adecuadamente a las nuevas exigencias del mercado que vienen delimitadas por la inconsistencia en el proceso flexográfico, la
dificultad en ajustar el color de impresión a la prueba, la falta de
predecibilidad en los resultados entre trabajos o repeticiones, la
tendencia al ensuciamiento de la impresión, las típicas roturas de
transiciones tonales, una densidad insuficiente o inestable, un espacio de color reducido,
preimpresión muy compleja y excesivos tiempos improductivos y
mermas por ajuste.
La tecnología LAM
Los puntos de la plancha digital LAM
tienen la cabeza redondeada y forma acampanada debido a la inhibición
del oxígeno en su formación. La superficie es propensa al desgaste,
especialmente los puntos de altas luces. Además, es fácil que se formen
puntos inestables y la impresión se hace impredecible. La
cabeza redondeada no define totalmente el área del punto y es propensa a
crecer por el efecto de la presión en máquina o por el comportamiento de
la tinta. Todo ello hace que la calibración se haga extremadamente difícil.
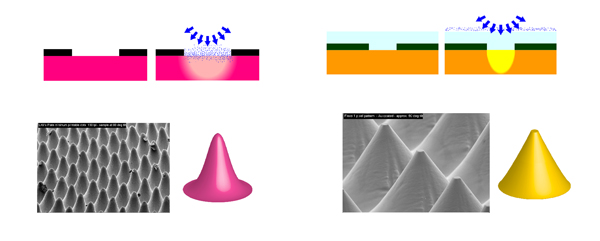
A la izquierda, inhibición por oxígeno
en la plancha digital tradicional (LAM, planchas digitales
tradicionales). La presencia del oxígeno durante la polimerización
inhibe la formación del punto y crea una estructura característica que
es sensible al desgaste y tiene un área de impresión poco definida. A
la derecha, el sistema Flexcel NX evita el efecto inhibidor del
oxígeno. La ausencia de oxígeno crea puntos de estructura consistente y
cabeza plana con superficie de impresión claramente definida de hasta 10
micrones de diámetro.
Flexcel NX consigue más con la flexografía
Kodak responde a las nuevas
exigencias del mercado y a las necesidades del impresor flexográfico
superando las limitaciones técnicas tradicionales, mejorando el impacto
visual, estabilizando la impresión, reduciendo los costes de producción y
disminuyendo los desechos.
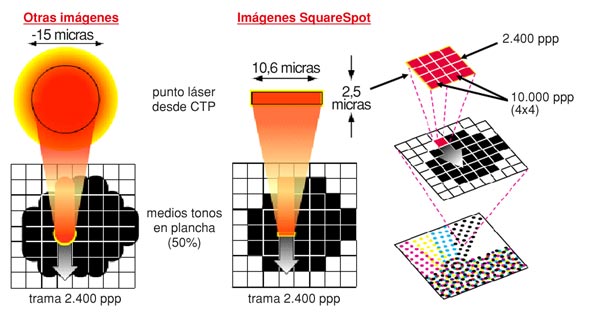
Tecnología de cabezal térmico Kodak Squarespot.
¿Qué es el sistema Flexcel NX?
El sistema Flexcel NX de Kodak consta
de:
CTP Kodak Trendsetter NX SquareSpot
Laminador Kodak Flexcel NX
Software Kodak TIFF Front End
Tecnología de texturización Kodak DigiCap
Film digital térmico de laminación TIL
Planchas flexográficas Kodak Flexcel NX
También:
Tecnologías de tramado Kodak (Maxtone, Hyperflex y Staccato Screening).
CTP Kodak Trendsetter NX SquareSpot
Laminador Kodak Flexcel NX
Software Kodak TIFF Front End
Tecnología de texturización Kodak DigiCap
Film digital térmico de laminación TIL
Planchas flexográficas Kodak Flexcel NX
También:
Tecnologías de tramado Kodak (Maxtone, Hyperflex y Staccato Screening).
El sistema Flexcel NX evita el efecto
inhibidor del oxígeno, ya que la ausencia de oxígeno crea puntos de
estructura consistente y cabeza plana con superficie de impresión
claramente definida hasta 10 micras de diámetro.
Al no existir oxígeno, tampoco hay
retracción del punto. La estructura adquiere forma de cono, con una base
abierta y resistente. La cabeza del punto es plana y con un tamaño y
forma idénticos al punto generado digitalmente. La reproducción es
1:1:1.
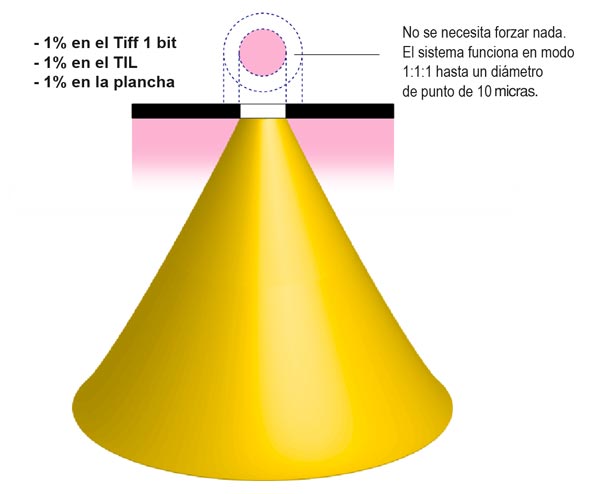
Las ventajas de la laminación NX.
La exactitud de la reproducción 1:1:1
permite dibujar en la plancha incluso la forma del propio pixel, con lo
que tenemos un amplio control y predicción de los resultados.
A diferencia de la plancha digital
LAM, la plancha digital Flexcel NX tiene un calibre idéntico en todo el
rango tonal e igual al de la altura de los sólidos, eso permite una
mayor uniformidad en las presiones de máquina.
La densidad del color, el otro desafío a superar
Existen limitaciones con las tintas,
especialmente con aquellas de base solvente sobre plásticos (densidad
insuficiente, transferencia de tinta deficiente y limitado espacio de
color). Dichas limitaciones significan una pérdida del impacto visual
respecto del huecograbado o una impresión carente de brillo. Además, en
ese contexto es necesario utilizar muchos colores especiales y dividir
un mismo color en varias planchas. Otra de las limitaciones es que suelen ser necesarias
tintas más caras o se requiere un mayor aporte en los anilox.
El desafío es conseguir una mejor
transferencia de tinta, ya que resolviendo los problemas con la
transferencia de tinta en sólidos y a lo largo de todo el rango tonal se
obtendrá un mejor resultado en la apariencia visual y contraste, se
reducirá la necesidad de colores especiales y se podrá imprimir a
mayores velocidades sin variaciones de densidad. Y en cuanto a costes,
los resultados serán mejores al mismo o menor precio.
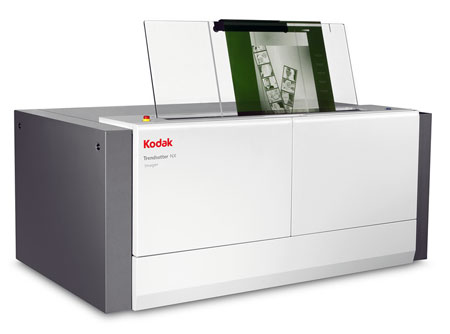
Sistema Kodak Flexcel NX.
¿Cuál es el problema con la plancha digital LAM?
La dificultad de controlar la correcta transferencia de tinta entre el anilox y la plancha y de la plancha al sustrato es uno de los principales problemas relacionados con la inconsistencia de la impresión flexográfica. La texturización de la superficie de la plancha es bien conocida como una alternativa para la mejora en la impresión de sólidos para casos concretos y se ha utilizado con diferentes métodos, tanto mecánicos como digitales, pero ninguno de ellos ha obtenido grandes progresos o ha resultado lo suficientemente consistente.
Kodak DigiCap NX Screening resuelve el problema.
Kodak DigiCap NX Screening aprovecha
la alta resolución del sistema NX para filmar y formar una microtextura a
lo largo de toda la superficie de impresión. El patrón es
extraordinariamente pequeño y uniforme (5x10 micras) y es aplicado en
todo el rango tonal. Se consigue a través de utilidad de software
incorporada al sistema NX y su aplicación es opcional y sencilla sobre
la filmación a través del control específico en el software Kodak Tiff
Front End.

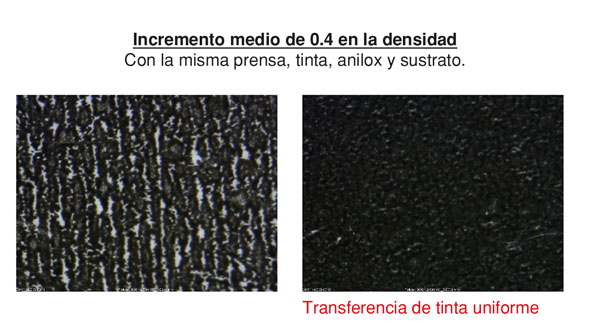
A la izquierda, plancha digital Flexo LAM sin texturización. A la derecha, plancha Flexcel NX con textura DigiCap NX.
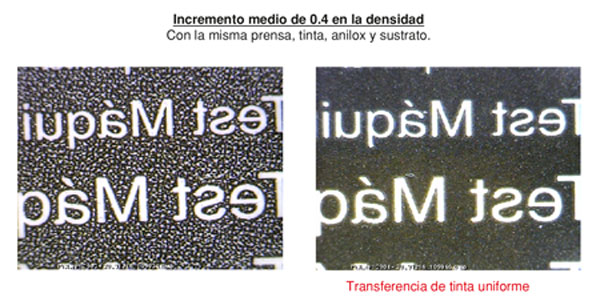
A la izquierda, plancha digital Flexo LAM con textura convencional. A la derecha, plancha Flexcel NX con textura DigiCap NX.
Kodak DigiCap NX no solo es para
áreas de sólidos. La alta densidad a lo largo de todo el rango tonal
significa expansión del gamut de color.
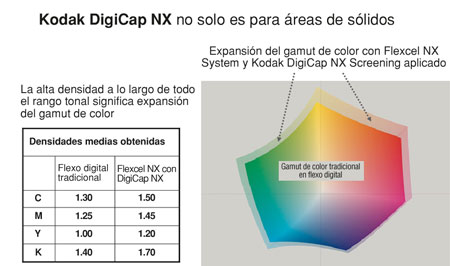
Ventajas de Kodak Flexcel NX:
- Impresión consistente de embalaje flexible con calidad de huecograbado.
- Impresión a mas de 200 lpi o uso de tramas estocásticas de 20 micras.
- Incremento de la densidad sin cambiar anilox o tinta.
- Alto contraste y rango tonal completo para impacto visual máximo.
- Expansión del gamut de color.
- Mayor número de colores especiales reproducibles en CMYK
- Puerta abierta a co-impresión de diseños.
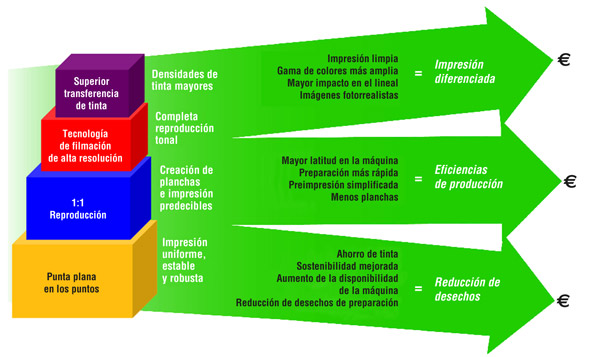
.
lunes, 8 de abril de 2013
Nuevos desafios del impresor flexográfico
Durante estos tres últimos años, tiempo que llevo como responsable de la cuenta de flexografia de Kodak en Iberia, he sabido reconocer el acierto de esta compañía al haber logrado percibir la realidad del sector flexográfico, focalizando los esfuerzos en el desarrollo de soluciones innovadoras que realmente se adapten a las nuevas tendencias que estaban y están llegando.
¿Qué tendencias son esas?. Desde mi punto de vista y creo que desde el del impresor de packaging en general, esas tendencias son las que marcan las necesidades del propietario de marca, cada vez mas condicionado por unos hábitos del consumidor muy dados al cambio y a verse afectados por diferentes factores, mas aún en estos tiempos en los que la crisis global está haciendo estragos en la economía familiar.
Es por este motivo que creo en que una tecnología de plancha orientada al impresor flexográfico debe ser capaz de responder principalmente a tres necesidades: la calidad de la impresión, la consistencia de esa calidad y su consecución dentro de unos costes predeterminados.
Cuando un profesional de la flexografía habla de calidad de la impresión, tal vez tenga tendencia natural a centrarse excesivamente en los aspectos artísticos del resultado: si este nos resulta agradable, si hemos conseguido unas transiciones tonales limpias, unos colores vivos, unos textos nítidos, etc. Sí..., ya sé que somos profesionales de las artes gráficas y las "Artes Gráficas" son también eso..., pero debemos recordar que un impresor flexográfico no tiene como meta la obtención de una "obra de arte", su meta es la consecución de los requerimientos establecidos por su cliente en base a unas "funcionalidades" concretas del envase. Entre esas funcionalidades, obviamente, están las relacionadas con el diseño gráfico y el color, ambos pensados explícitamente para captar la atención del consumidor en el punto de venta. Y en esto estamos..., pero no podemos obviar otros valores que son fundamentales; como el ser capaces de poder mantener ese buen resultado de manera estable durante toda la tirada, poder repetirlo en una segunda o tercera entrada en máquina, implementar este resultado como un estándar para el resto de trabajos o garantizar el respeto a la marca, siempre sin olvidar que esos resultados deben ser obtenidos con unos costes limitados y dentro de unos parámetros medioambientales establecidos.
Kodak entendió esto muy bien y decidió diseñar una herramienta capaz de sacar a la flexografía de alto nivel de un estancamiento que le impedía responder adecuadamente a estos nuevos desafio. Y Kodak Flexcel NX nació para responder de manera adecuada a esas tres necesidades del impresor que comentaba anteriormente:
1.- La calidad de la impresión.
Dotando al impresor de un concepto de plancha de alta definición, capaz de ofrecer una capacidad de reproducción del 100% (hasta el mismo pixel del archivo digitaL), con puntos de estructura estable, con diametros de hasta 10 micrones que llevan las posibilidades de reproducción en plancha hasta el rango tonal completo con lineaturas de hasta 300Lpi.
2.- La consistencia.
Si en algo se ha caracterizado la flexografía a lo largo de los años ha sido en su inconsistencia, sobre todo cuando los requerimientos de calidad exceden de un cierto nivel. Con los nuevos requerimientos existentes, esa inconsistencia se ha convertido en el principal desafío para un impresor flexográfico, entre otras cosas por que es lo que suele determinar la viabilidad y rentabilidad del tiraje.
Esa inconsistencia viene principalmente dada por las variables que afectar a la propia reproducción de la imagen en la plancha, a su integridad durante el proceso de impresión y al modo en el que transmitimos esa imagen en el sustrato.
Kodak Flexcel NX, con su insuperable capacidad de reproducción del archivo digital, la estructura de punto cónico con cabeza plana y la increiblemente precisa microtexturización DigiCap de 5 micras en la superficie de tramas y sólidos, permiten obtener un resultado estable y definido, con transiciones limpias y con colores intensos para un resultado realmente predecible en flexografía. Todos ellos son aspectos fundamentales para garantizar esa consistencia y establecer un estándar de calidad acorde con las necesidades de marca.
3.- Los costes.
Un concepto de impresión poco predecible e inconsistente es un agujero sin fondo en términos de coste para un impresor. En la medida que controlamos y reducimos los tiempos de ajuste, las paradas de máquina, la carga de tinta, la utilización de mas pigmentación, las mermas de ajuste en sustrato y tintas, las horas del tiraje, los costes de energía, el número de colores o extendemos la durabilidad de las planchas, generamos una ahorro en los costes que es vital y definitivo para el impresor.
Si nos fijamos en todos estos puntos, veremos que la mayoría de ellos, por no decir todos, guardan directa o indirectamente relación con el funcionamiento de la plancha en el cuerpo impresor. Kodak ha resuelto eficazmente muchos de estos problemas con Flexcel NX, llevando a la impresión flexográfica, de manera real e indiscutible, a las cotas de calidad y rentablidad que exige hoy en día el mercado.
¿Qué tendencias son esas?. Desde mi punto de vista y creo que desde el del impresor de packaging en general, esas tendencias son las que marcan las necesidades del propietario de marca, cada vez mas condicionado por unos hábitos del consumidor muy dados al cambio y a verse afectados por diferentes factores, mas aún en estos tiempos en los que la crisis global está haciendo estragos en la economía familiar.
Es por este motivo que creo en que una tecnología de plancha orientada al impresor flexográfico debe ser capaz de responder principalmente a tres necesidades: la calidad de la impresión, la consistencia de esa calidad y su consecución dentro de unos costes predeterminados.
Cuando un profesional de la flexografía habla de calidad de la impresión, tal vez tenga tendencia natural a centrarse excesivamente en los aspectos artísticos del resultado: si este nos resulta agradable, si hemos conseguido unas transiciones tonales limpias, unos colores vivos, unos textos nítidos, etc. Sí..., ya sé que somos profesionales de las artes gráficas y las "Artes Gráficas" son también eso..., pero debemos recordar que un impresor flexográfico no tiene como meta la obtención de una "obra de arte", su meta es la consecución de los requerimientos establecidos por su cliente en base a unas "funcionalidades" concretas del envase. Entre esas funcionalidades, obviamente, están las relacionadas con el diseño gráfico y el color, ambos pensados explícitamente para captar la atención del consumidor en el punto de venta. Y en esto estamos..., pero no podemos obviar otros valores que son fundamentales; como el ser capaces de poder mantener ese buen resultado de manera estable durante toda la tirada, poder repetirlo en una segunda o tercera entrada en máquina, implementar este resultado como un estándar para el resto de trabajos o garantizar el respeto a la marca, siempre sin olvidar que esos resultados deben ser obtenidos con unos costes limitados y dentro de unos parámetros medioambientales establecidos.
Kodak entendió esto muy bien y decidió diseñar una herramienta capaz de sacar a la flexografía de alto nivel de un estancamiento que le impedía responder adecuadamente a estos nuevos desafio. Y Kodak Flexcel NX nació para responder de manera adecuada a esas tres necesidades del impresor que comentaba anteriormente:
1.- La calidad de la impresión.
Dotando al impresor de un concepto de plancha de alta definición, capaz de ofrecer una capacidad de reproducción del 100% (hasta el mismo pixel del archivo digitaL), con puntos de estructura estable, con diametros de hasta 10 micrones que llevan las posibilidades de reproducción en plancha hasta el rango tonal completo con lineaturas de hasta 300Lpi.
2.- La consistencia.
Si en algo se ha caracterizado la flexografía a lo largo de los años ha sido en su inconsistencia, sobre todo cuando los requerimientos de calidad exceden de un cierto nivel. Con los nuevos requerimientos existentes, esa inconsistencia se ha convertido en el principal desafío para un impresor flexográfico, entre otras cosas por que es lo que suele determinar la viabilidad y rentabilidad del tiraje.
Esa inconsistencia viene principalmente dada por las variables que afectar a la propia reproducción de la imagen en la plancha, a su integridad durante el proceso de impresión y al modo en el que transmitimos esa imagen en el sustrato.
Kodak Flexcel NX, con su insuperable capacidad de reproducción del archivo digital, la estructura de punto cónico con cabeza plana y la increiblemente precisa microtexturización DigiCap de 5 micras en la superficie de tramas y sólidos, permiten obtener un resultado estable y definido, con transiciones limpias y con colores intensos para un resultado realmente predecible en flexografía. Todos ellos son aspectos fundamentales para garantizar esa consistencia y establecer un estándar de calidad acorde con las necesidades de marca.
3.- Los costes.
Un concepto de impresión poco predecible e inconsistente es un agujero sin fondo en términos de coste para un impresor. En la medida que controlamos y reducimos los tiempos de ajuste, las paradas de máquina, la carga de tinta, la utilización de mas pigmentación, las mermas de ajuste en sustrato y tintas, las horas del tiraje, los costes de energía, el número de colores o extendemos la durabilidad de las planchas, generamos una ahorro en los costes que es vital y definitivo para el impresor.
Si nos fijamos en todos estos puntos, veremos que la mayoría de ellos, por no decir todos, guardan directa o indirectamente relación con el funcionamiento de la plancha en el cuerpo impresor. Kodak ha resuelto eficazmente muchos de estos problemas con Flexcel NX, llevando a la impresión flexográfica, de manera real e indiscutible, a las cotas de calidad y rentablidad que exige hoy en día el mercado.
jueves, 4 de abril de 2013
Jornada Flexográfica de KODAK en Barcelona en 18 de Abril frente a Graphispag Digital
Me complace mucho informaros de que coincidiendo con la celebración del evento Graphispag Digital, donde Kodak tendrá un stand con sus novedades en este ámbito, organizaremos también una jornada técnica sobre flexografía en el Hotel FIRA CONGRESS, ubicado justo frente a la feria. En esta jornada tendré ocasión de presentar las distintas soluciones que Kodak está introduciendo con un extraordinario éxito en el sector flexográfico y en concreto sobre Flexcel NX, que ha roto los esquemas que teníamos establecidos convirtiendose en el nuevo estándar de la alta calidad y productividad y en el referente a seguir.
No solo tendremos ocasión de presentar esta exitosa tecnología, sino también la solución Kodak Flexcel Direct Engraving, el sistema de grabación de camisas en continuo y planchas en modo directo 3D que sorprendió durante Drupa y con el que Kodak propone un nuevo concepto de grabación directa basada en la alta productividad, la calidad y la reducción de costes.
Si estáis interesados en asistir podéis dirigiros a mi email: miguelangel.beltran@kodak.com y con gusto os haré llegar un link para que podáis inscribiros. Os adelanto el folleto promocional de esta jornada en el que veréis las temáticas que abordaremos.
Os espero.
Suscribirse a:
Entradas (Atom)